Understanding the Fundamentals and Applications of Plastic Extrusion in Modern Manufacturing
In the realm of contemporary production, the method of plastic extrusion plays an instrumental role - plastic extrusion. This complex procedure, including the melting and shaping of plastic with specialized passes away, is leveraged throughout different industries for the development of varied products. From auto parts to consumer products product packaging, the applications are huge, and the potential for sustainability is just as excellent. Deciphering the principles of this process discloses the real flexibility and capacity of plastic extrusion.
The Principles of Plastic Extrusion Process
While it may show up facility, the principles of the plastic extrusion process are based on reasonably uncomplicated concepts. It is a manufacturing procedure in which plastic is melted and then formed right into a continuous account via a die. The plastic extrusion procedure is extensively used in numerous sectors due to its cost-effectiveness, flexibility, and effectiveness.
Various Types of Plastic Extrusion Strategies
Building upon the standard understanding of the plastic extrusion procedure, it is required to discover the various techniques associated with this manufacturing approach. The 2 main strategies are profile extrusion and sheet extrusion. In profile extrusion, plastic is thawed and formed into a continual profile, usually used to produce pipelines, rods, rails, and window frameworks. In comparison, sheet extrusion develops large, level sheets of plastic, which are commonly further refined into products such as food product packaging, shower curtains, and car parts. Each method calls for specialized machinery and specific control over temperature level and pressure to make sure the plastic keeps its form during cooling. Recognizing these techniques is essential to making use of plastic extrusion effectively in modern manufacturing.

The Role of Plastic Extrusion in the Automotive Sector
An overwhelming majority of parts in modern-day automobiles are items of the plastic extrusion process. This procedure has reinvented the automotive industry, transforming it into an extra reliable, economical, and versatile production field. Plastic extrusion is mostly used in the production of various auto elements such as bumpers, grills, door panels, and dashboard trim. The process gives an uniform, regular output, enabling makers to produce high-volume get rid of terrific precision and very little waste. The agility of the extruded plastic components contributes to the general decrease in lorry weight, enhancing fuel performance. Moreover, top article the resilience and resistance of these parts to warm, cool, and influence enhance the durability of autos. Hence, plastic extrusion plays a critical duty in automobile Read Full Report production.

Applications of Plastic Extrusion in Consumer Item Manufacturing
Beyond its considerable impact on the auto industry, plastic extrusion confirms equally efficient in the world of customer goods producing. The versatility of plastic extrusion enables manufacturers to create and generate complex forms and sizes with high precision and performance. The versatility, flexibility, and cost-effectiveness of plastic extrusion make it a preferred choice for lots of consumer goods makers, contributing significantly to the sector's growth and development.
Ecological Impact and Sustainability in Plastic Extrusion
The pervasive usage of plastic extrusion in manufacturing invites examination of its ecological ramifications. As a process that often uses non-biodegradable products, the ecological influence can be substantial. Energy consumption, waste manufacturing, and carbon emissions are all issues. Sector developments are raising sustainability. Effective equipment decreases power usage, while waste monitoring systems reuse scrap plastic, lowering resources needs. In addition, the growth of biodegradable plastics offers a more eco-friendly option. In spite of these renovations, even more development is needed to alleviate the ecological impact of plastic extrusion. As society leans towards sustainability, manufacturers should adapt to continue to be sensible, emphasizing the relevance of continual research and advancement in this field.
Final thought
To conclude, plastic extrusion plays a critical duty in contemporary manufacturing, especially in the auto and consumer products industries. Its adaptability permits the production of a large range of elements with high accuracy. In addition, its capacity for reusing and development of naturally degradable materials uses an appealing avenue towards sustainable techniques, therefore attending to ecological issues. Comprehending the fundamentals of this procedure is essential to maximizing its advantages and applications.
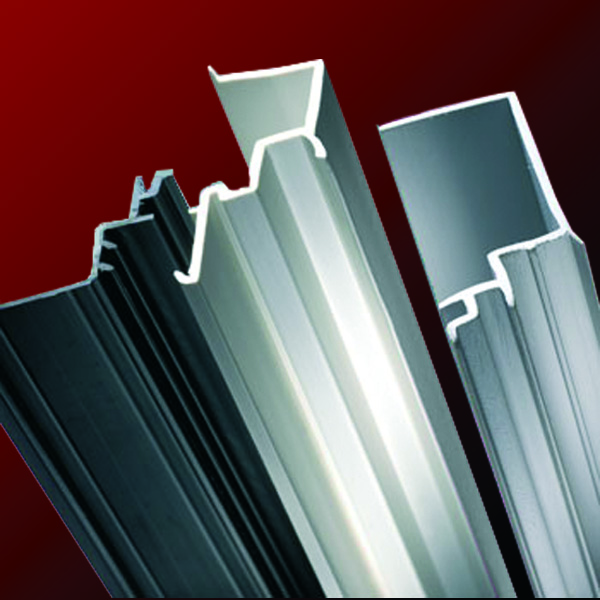
The plastic extrusion process is extensively utilized in various markets due to its flexibility, cost-effectiveness, and effectiveness.
Building upon the standard understanding of the plastic extrusion process, it is needed to check out the various methods find out here now included in this manufacturing approach. plastic extrusion. In contrast, sheet extrusion develops big, flat sheets of plastic, which are usually more refined into products such as food product packaging, shower curtains, and vehicle components.A frustrating bulk of components in modern automobiles are items of the plastic extrusion procedure